By Bill Bregar SENIOR STAFF REPORTER Published: October 23, 2014 2:39 pm ET Updated: October 23, 2014 2:44 pm ET
Image By: Bill Bregar W. Amsler Equipment Inc. won first place in the Society of Plastics Engineers' Blow Molding Division's awards contest for its triangular bottles.
CHICAGO — The Society of Plastics Engineers’ Blow Molding Division presented awards to packaging innovations like triangular bottles, flask containers for Jack Daniels, an industrial products line a game table and a giant ice cooler.
Judges selected winners from 14 entries, at the SPE Blow Molding Conference, held Oct. 5-7 in Chicago. This was the second annual blow molded parts competition.
Here is a recap of the awards:
Packaging
First place: W. Amsler Equipment Inc. of Richmond Hill, Ontario, won for a set of four triangular-shaped PET bottles that nest together for efficient packaging. Retailers also save space. The bottles use recycled food-grade PET to replace PVC.
The blow molder is Salboro Bottle, using a mold from V.P. Tool & Mold.
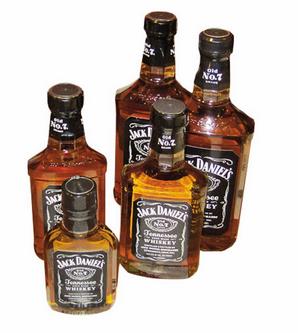
Image By: Bill Bregar Amcor Rigid Plastics made PET flasks for Jack Daniels.
Second place: PET Jack Daniels flask containers in four sizes, molded in a two-step process by Amcor Rigid Plastics USA Inc. at Amcor’s plant in Nicholasville, Ky. Hallink RSB Inc. made the molds.
Third place: The Glassa Ponti squeezable PET bottle for cooking glazes made by Italy-based Ponti SpA, which is the blow molder. The blow molding machinery supplier is Sipa SpA. The package was converted to a squeezable, slightly oval-shaped PET bottle from a non-squeezable HDPE bottle.
Industrial
First place: The Esky 135-quart cooler, a big HDPE cooler blow molded by Coleman Co. Inc. and designed to compete against the Yeti brand of rotationally molded coolers. It holds ice for up to two weeks. The mold maker is Hawkeye Preferred Tooling Group. Judges admired the special slides on the mold needed to make the drain at the bottom of the deep-draw part.
Second place: From designers Ed Wu and Alex Lopex, the Buzz Ball Football game table is designed for playing the sliding-triangle football game. Tackoffs were configured to offset a challenging blow area on the top of the table. An extra deep structure was designed in to overcome warping issues. The table has adjustable folding legs. A plastics designer, Wu runs 99studio Inc. in Naperville, Ill. Lopez is at Amiplex Inc. in Miami, Fla. SPI Industries’ blow molding plant in Coloma, Mich., molds the HDPE table. The mold maker is Ram Pattern Inc. of LeClaire, Iowa.
Third place: The Water Walker, a large U-shaped flotation device designed for duck hunters, fishermen and trappers to keep them safe in the water — and their guns dry. Agri-Industrial Plastics Co. in Fairfield, Iowa, is the molder. H&H Mold and Tooling Inc. in Fairfield made the mold.
Image By: Bill Bregar Ed Wu was part of a team that won an award for the Buzz Ball Football game table.
Category Award for Industrial: An anesthesia breather bag, a collapsible TPE reservoir used during general anesthesia or artificial ventilation. The manufacturer is Intersurgical Ltd. of Berkshire, England. FGH Systems Inc. of Denville, N.J., made the mold, and a special cutting device to trim flash from the neck without the need for a secondary post-trimming step.
Category Award for Beverage Packaging: A 55-ounce PET wide-mouth jar molded by Amsler Equipment Inc. using two-step stretch blow molding from a parison, then spin trimmed. Two-step blow molding gives four times higher output per mold than the one-step stretch blow process, and it uses less resin because of the lighter neck finish.
Category Award for Pharmaceutical Packaging: A Johnson & Johnson Baby Powder container that reduces cost by only using the polypropylene bottle and the cap, instead of a labeled-cap and shrink band on the bottle used previously. The new cap is flip-top for one-hand use. The blow molder is Creative Group of Industries Ltd. of Mumbai. The South Korean mold maker is Alchemy Molds & Plastic Ltd
People’s Choice
Beverage Packaging, for the Tropicana handleware bottle blow molded from extrusion-grade PET. It sported a special two-piece closure. Graham Packaging Co. LP is the blow molder, and AptarGroup Inc. molds the preform.
Industrial, to the parking lot block, blow molded and foam filled in the one-step FoamCore process. Pinnacle Plastic Products Inc. blow molds the polypropylene, foam-filled parking blocks from a mold made by PT Tech.
|